In this post I’ll explain in detail how you too can turn your fancy Deluxe Game Chief’s “Handbrain” Screen from slick, dry-erase-compatible ABS plastic to a battered, rusty piece of equipment that has seen better centuries.
A Disclaimer Meant to Give You Hope
Sandra did all the modding work shown here, and she is a beginner. I explained the processes and provided tools, but she is the one who applied all the paint. This was her second experience with spray paint, and her first experience with glazing and dry-brushing, so while the results are perhaps a bit less polished than if I’d done the work, they’re easily within the reach of somebody who is new to hobby painting.
This tutorial is long, but the actual process goes very quickly, and most of the time you spend on the project will be spent waiting for things to dry between steps.
Let’s go!
Modding Your Handbrain
Supplies & Tools

You will need the following:
- The Handbrain Screen (or anything else that will take spray paint, and that needs to look rusty)
- Two large pieces of cardboard (work surfaces)
- Paper towels
- Letter or A4 paper, folded or cut in half.
- Scissors
- CA glue (“Superglue”)
- Sandpaper or a sanding sponge
- Ultra-flat black spray paint (Rustoleum® Camoflage Black is my favorite)
- Testors Dullcote spray lacquer
- P3® hobby paints: “Bloodstone” and “Pig Iron”
- Two paint brushes—one for the rust wash, and one for dry-brushing.
- Water for thinning paint and rinsing brushes
- Q-tips (not shown in photo)
- Something to mix paint on (not shown in photo. Sandra used a paper plate.)
With the exception of the paint, brushes, and sanding sponge, everything here is probably already in your house. If not, the total cost of these supplies is between $20 and $30, unless you go all-in on fancy brushes, which we did not.
The P3 paints are available from your friendly local game store, and from lots of online shops as well. Each bottle costs about $4. Any metallic acrylic hobby paint can be used in place of the Pig Iron, but I have not found an acceptable “rust wash” substitute for Bloodstone.
Phase 1: Surface Prep
In which we add a little of our own texture to the surface, and get it ready for paint.
- Sand the corners of the screen
- If you’re feeling really plucky, take the scissors and score some “battle damage” in places.
- Wipe it down with a damp paper towel, and then wipe it dry. This is the only critical step here. The sanding and scoring is just for show.
Phase 2: Patch and Customize
Superglue + paper = welded metal patch
- Cut paper patches for the eight holes in the corners of the screen.
- DO ALL GLUE THINGS ON DISPOSABLE CARDBOARD WORK SURFACE. Because superglue is forever.
- Carefully, drop-by-drop, create a bead of superglue around the hole.
- Lay a paper patch over the hole. It will wick up the glue and change color.
- Using a Q-tip, flatten the paper. As necessary, add another drop of superglue, and spread that with the Q-tip.
- Repeat steps 3-5 for the remaining 3 corners on this face.
- Wait for the glue to dry. It will dry faster in humid environments because superglue does not “dry,” it “cures” by bonding with water. (This, incidentally, is why you don’t wash wet superglue from your body using water. Wipe it off with a dry paper towel. The driest you can find, but be quick…)
- Flip the screen over, and repeat steps 3-7 for the four corner holes on the back.
- Feeling plucky? Cut some more paper into cool shapes, and glue those down. By now you’ll feel pretty confident in your process. Sandra did!
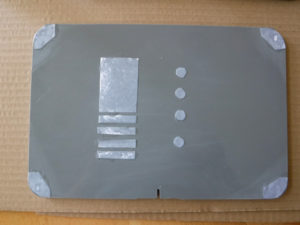
Phase 3: Spray Paint!
If you’ve spray-painted things before this whole section will seem like too many words.
Find a good place, like and outdoor place, to paint. Use your cardboard to prevent painting things that should remain unpainted.
- Stand the screen on its base, and insert a sheet of paper to mask the inside surface of the screen.
- Apply spray paint to the front of the screen and the back of the base (but not the back of the screen) according to the instructions on the can
- Wait for it to dry. Ten to twenty minutes, unless you over-sprayed and made puddles. The ultra-flat finish paint is only shiny when it’s still wet, so you don’t need to touch the surface to check for dryness.
- Flip screen in stand. Paint the back of it (now that it’s at an angle which is easy to get at.)
- Again, the waiting.
Remove the screen from the stand. See the bit that was masked by the base? Very lightly spray that part, front and back.
- More waiting.
- Ready for Phase 4!
Phase 4: Getting Rusty
Thanks to quirks in the formulation of P3 Bloodstone, this step is like magic. It looks terrible, and then suddenly it looks perfect.
- Closely consider this picture of wet paint.
- The upper puddle is P3 Bloodstone with a little water in it. The lower puddle is water with a little P3 Bloodstone in it. You’ll be using the lower puddle.
Get your brush sopping wet in the watery Bloodstone puddle. Generously apply that to the Handbrain. You’ll need several brushloads to get the job done.
- Keep going until the whole front face is wet, and you’ve got decent puddles hugging the details of the screen (including the details you made with paper and superglue.)
- Wait for it to dry. While you wait, look at these two pictures:
The back of the handbrain, before and after the Bloodstone wash has dried. - Feeling better about the mess? Keep waiting for it to dry. You’ll know it’s dry when you begin wondering where this rusty piece of metal came from.
- Repeat steps 3-5 on the back of the screen, complete with more waiting. Also, do the stand now.
This is what the back of Sandra’s screen looked like in bright light. That’s ABS plastic, superglue, and paint. No slabs of iron were oxidized in the making of this photo.
Phase 5: Shiny Metal Shows Through
In which you learn to drybrush, and possibly get frustrated about having ruined the whole thing, but that’s normal because there’s a learning curve.
- Read this aloud: “Learning to drybrush will take a few minutes, and even if I already know how to do it on miniatures, drybrushing something big and flat may prove different.”
- Look at this picture (click to enlarge). It is from Sandra’s first-ever drybrushing, and it has awesome bits, and some mistakes.
- Realize that by showing you our mistakes, we’re giving you permission to make a whole bunch of your own. Relax…
- Get a little paint on your big brush.
- With a rapid, back-and-forth motion, paint the paper. You’re getting all the wet paint off the brush, and getting air between the bristles. Keep going until no more paint blotches appear.
- Pick up the stand (not the screen) and with that same motion, brush against the “grain” of the screen, your strokes moving at 90° to any raised edges or details. You’ll know you’re doing it right when the edges look shiny, but the flat areas have very little metallic sheen to them.
- When the shine no longer appears as you brush it is time to reload your brush. Repeat steps 4-5.
- Aren’t you glad you practiced on the small piece? Feeling confident? Good.
- Pick up the screen, and drybrush it until you’ve made all the edges shine from the wear-and-tear that shaves oxidized metal away, and polishes what’s underneath.
Here’s what Sandra’s looks like without the paper mask in place. The grey is naked ABS plastic. The rusty metal is not actually metal. Neat, huh?
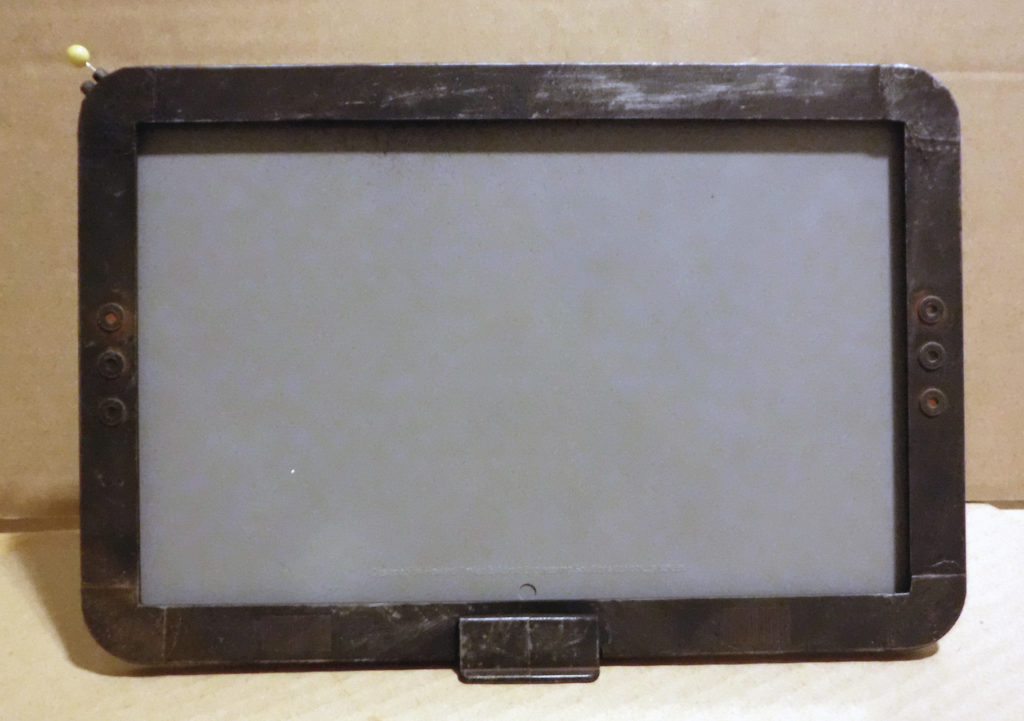
Phase 6: Make It Durable
Because you want to play with it, not just put it up on a shelf for display, right?
- Return to your spray-painting place. It needs to be ventilated well, because this paint is pretty smelly.
- If you removed it the paper from the screen, put it back in now.
- Lightly spray the screen and its base with Testor’s Dullcote spray lacquer.
- Make sure to spray the part where the base covers the screen.
- Let it dry.
Testors Dullcote is my absolute favorite protective finish for models like this. It drys to leave a very flat, matte finish. Reflected light won’t be obscuring the paint job you worked so hard on. It shows off your work, while protecting the model from ordinary wear-and-tear. I like it so much I’ll totally shill for it, as evidenced by the linked text. I’ve used other matte finishes, but none are as purely non-reflective as Testor’s.
Summary
I often refer to this process in a way that omits all the persnickety details: “base coat, wash, drybrush, done.” For folks familiar with the hobby, that’s enough to get the point across.
This process works quite well on 28mm miniatures. Often I’ll start by doing the rusty look, and then add colors to the parts of the mini that are not supposed to be weathered metal. Sometimes I’ll forget that the model isn’t actually finished, and it’ll stay in the rusty metal state for several years. Yes, Cygnar Lancer warjack, I’m looking at you. As is everyone else…
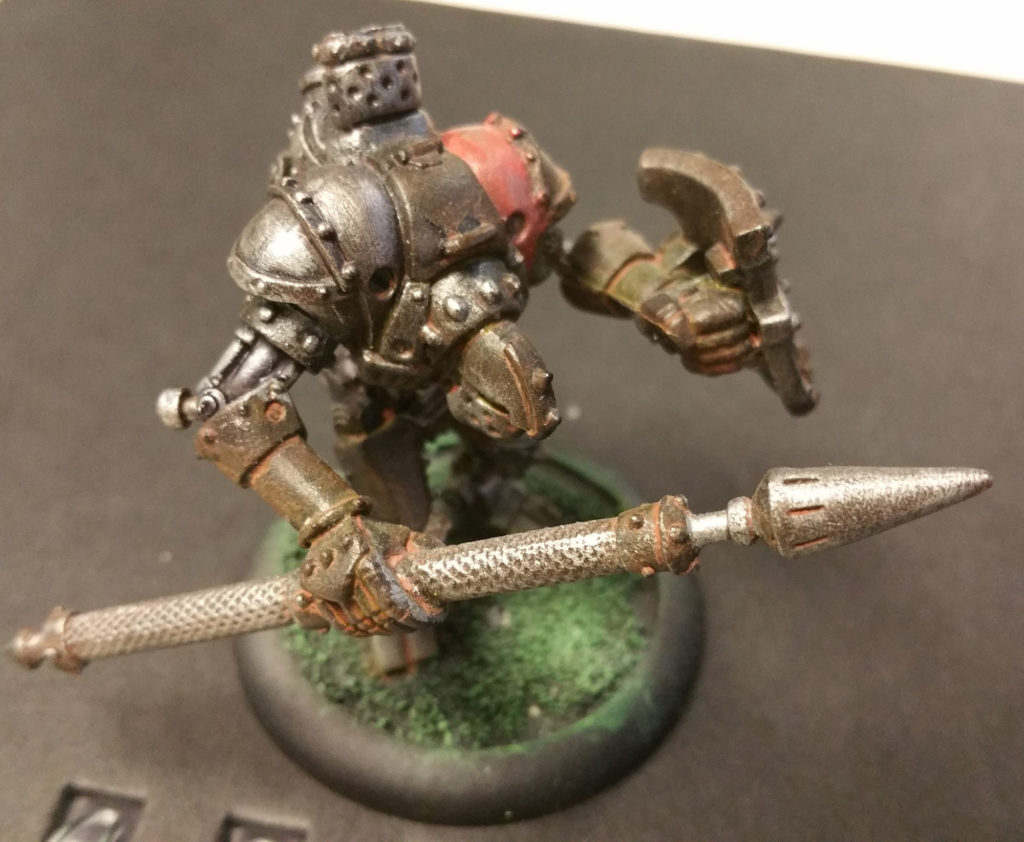
It’s not the only way to get this look, and it’s not even necessarily the best way, but after lots of experimentation, it strikes the right balance between “easy” and “the right look,” at least for me.